Employee involvement turn LTP into 'wow-factory'
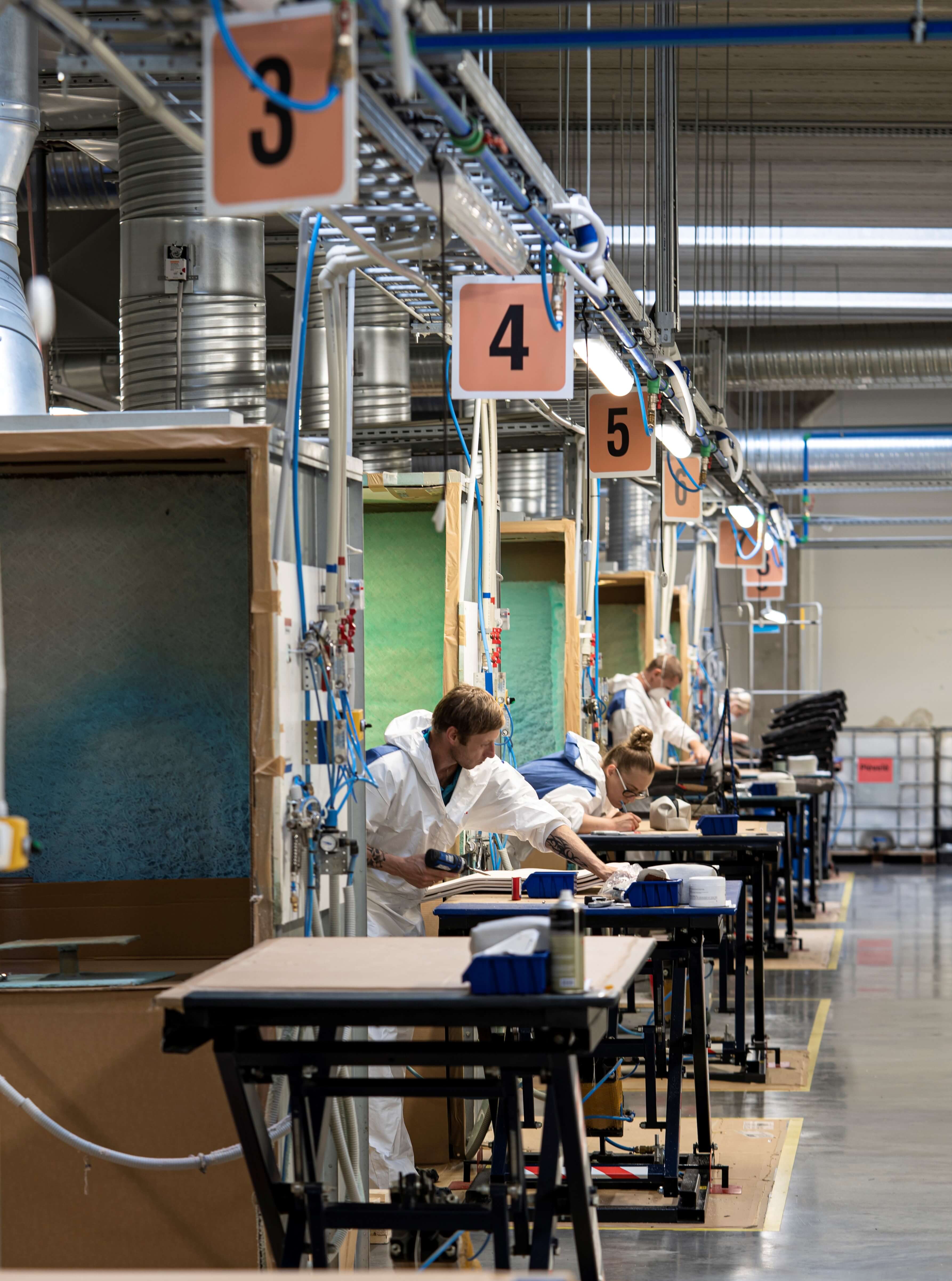
LEAN at LTP comes down to understanding customer value – it’s that simple! The ultimate goal is to provide perfect value to the customer through a flawless and super-optimized value creation process.
To accomplish this, LEAN thinking was implemented in Texdan in 2019. Vygandas Venzlauskas, Production Manager, explains how it all started:
“10 years ago, I merely understood LEAN as yellow lines on the floor and tidy order at the working-stations. I saw it is my responsibility to keep it clean and safe. But that didn’t change anything. Today I understand, that the key is to change the focus of management from optimizing separate technologies, assets, and vertical departments - to optimizing the flow of products and services through entire value streams, that flow horizontally across technologies, assets, and departments.
We needed to engage our colleagues!”
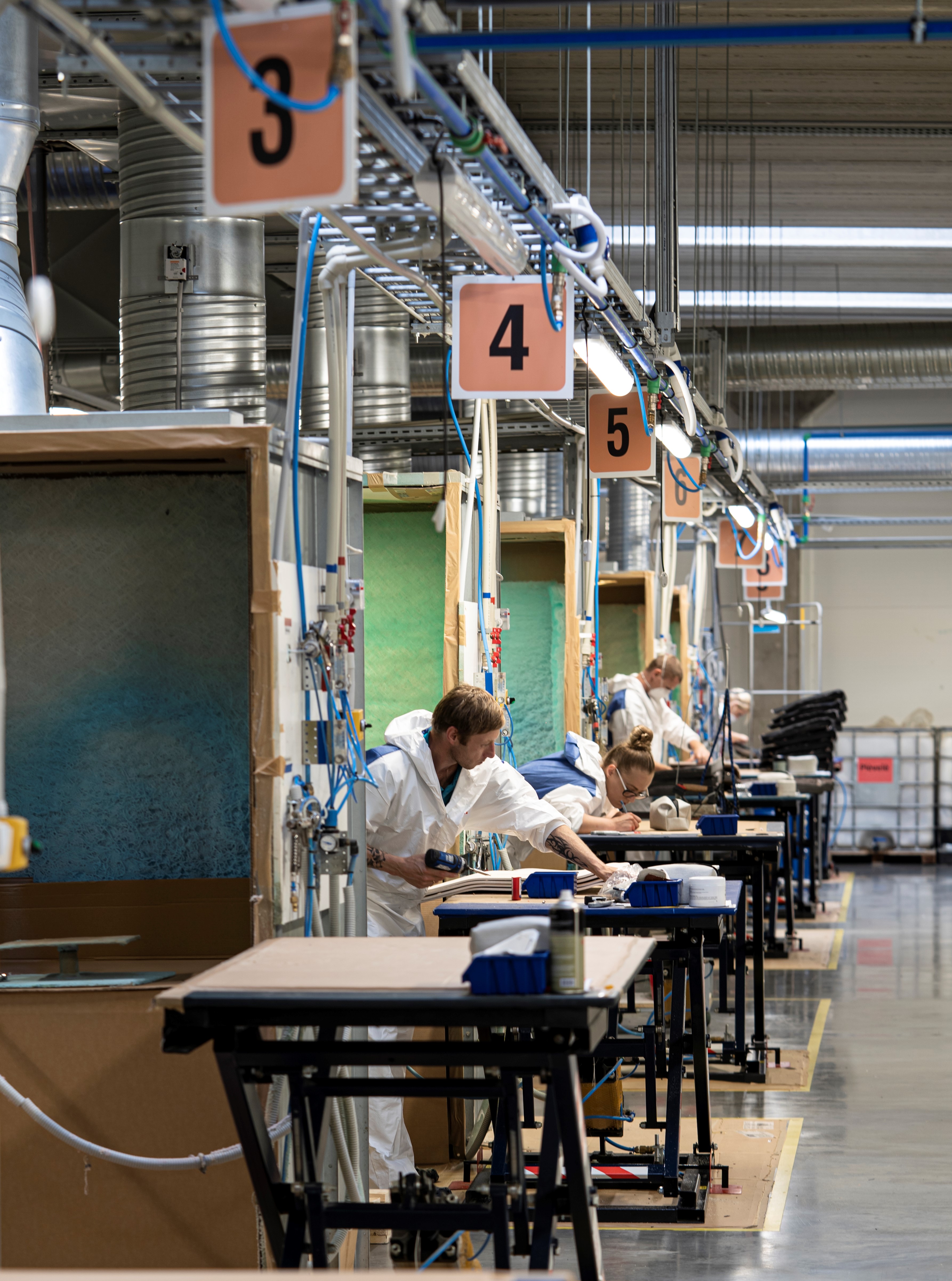
The LEAN culture today
Today more than 200 people are engaged in LEAN practices, and 5 LEAN leaders have been appointed - as a natural acknowledgement of the fact that the valuable input comes from ‘the floor’. It is now also their responsibility to solve issues and detect areas of optimization.
Vygandas continues:
“LEAN is a way of thinking and acting for the entire organization. We respect each other on all levels – listen to whatever problems are raised. Now, the employees are solving these problems, and the Managers only supervise and optimize on over all operations. The employees are handed responsibility – so they can solve problems themselves. Our vision with LEAN is to build a WOW factory, which is state of the art in furniture production”
Tools implemented
LEAN has an extensive collection of tools and concepts, but for our Furniture production facility the perfect fits have been chosen, to optimize every aspect possible to secure a LEAN production, beneficial for the customers.
5S –visual management/organizing the work-area
Sort, Set In Order, Shine, Standardize and Sustain.
5S eliminates ‘waste’ that results from a poorly organized work area (e.g. wasting time looking for a tool).
Everything from tools to safety guiding around the facilities are optimized.
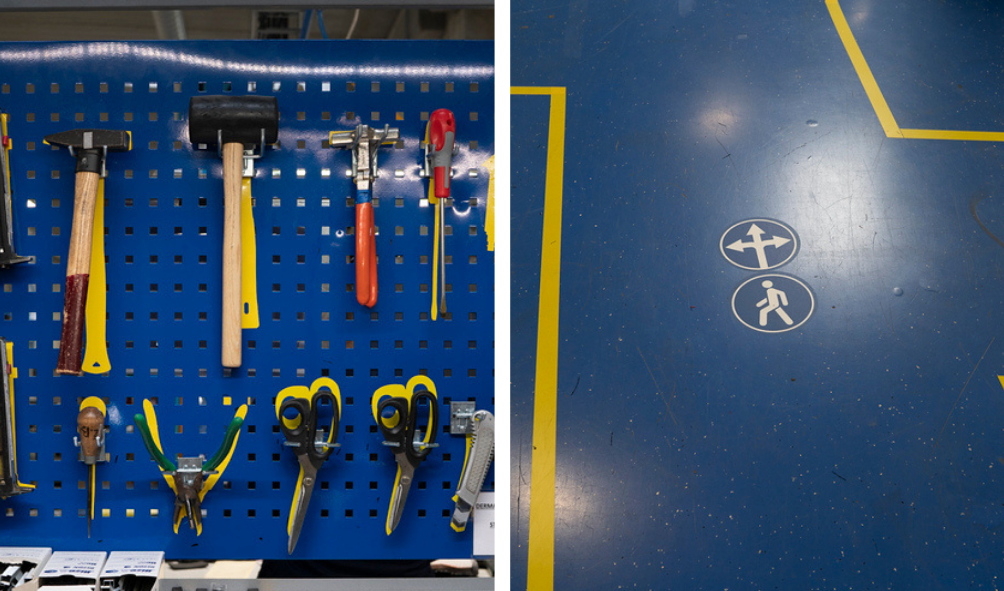
Kaizen– continuous improvement
The strategy where our employees work together proactively to achieve regular, incremental improvements in the manufacturing process. Kaizen combines the collective talents of LTP to create an engine for continually eliminating ‘the 7 types of waste’ from our manufacturing processes. All ideas are welcomed on the board and discussed every week.
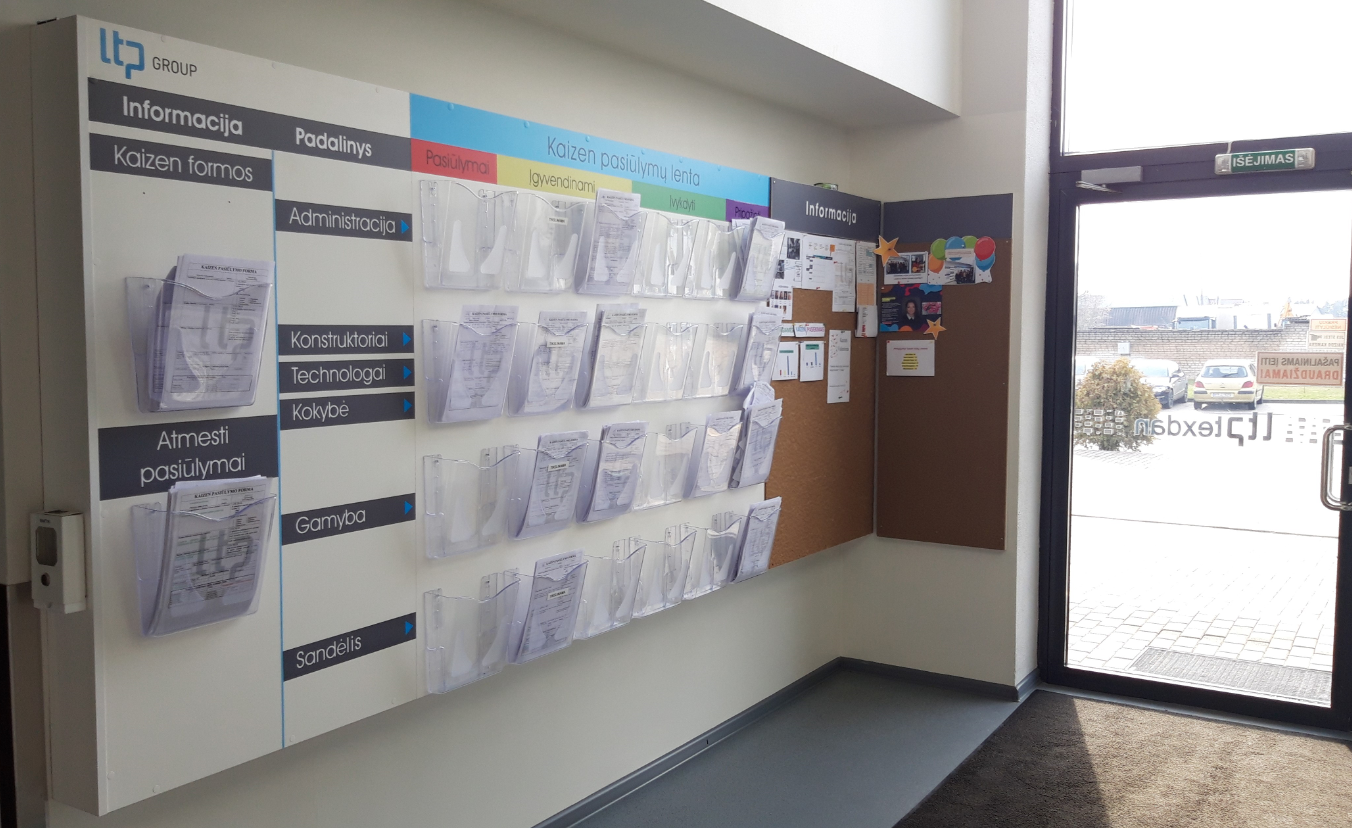
Asaichi – Meetings
This is our daily standing meeting with representatives from all departments. The information comes from the employee sand goes up. A complete run-though of all areas – accidents, quality, mistakes etc. During these short and effective meetings, continuous monitoring of the main indicators is carried out, the problem is identified, and responsible persons are appointed for its solution. This is a great opportunity to praise our employees handling of issues, to further enhance their motivation.
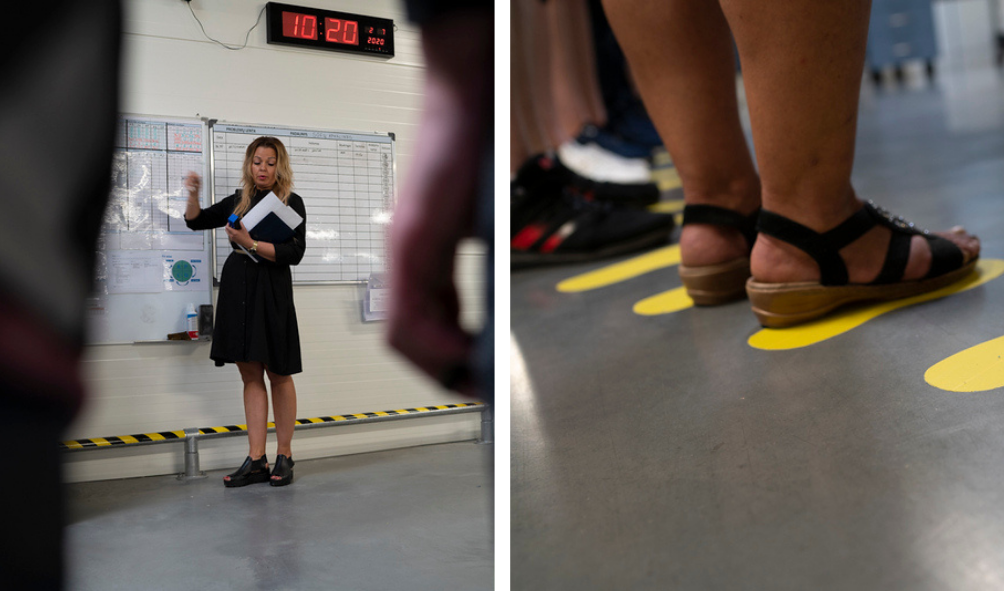
TWI – Training within industries
This is planned to fully set in to action during 2021. It is an essential element in sustaining LEAN initiatives in manufacturing. It provides our frontline personnel with the skillset to establish a culture for change, process to achieve standard work, framework for continuous improvement, and easy-to-apply methods to achieve results.
In LTP it’s used for purposes such as education and training.
How does LEAN benefit the customers
Simply, LEAN means creating more value for customers with fewer resources.
It is a win-win that constantly keep us on our toes. The ‘wow-factory’ expresses a high-speed, clean, lean and safe production factory. The out-put is second-to-none quality products and happy customers.
Vygandas concludes:
“And on top of that, the employees are motivated by being involved in the processes. They gain responsibility and are being recognized. This combined – it would be fair to say that we have a ‘wow-factory’”
Please feel free to contact LTP regarding questions about the LEAN culture.
vygandas@ltpgroup.com