Cellulosics and Circularity: The New Generation of Alternative Fibers
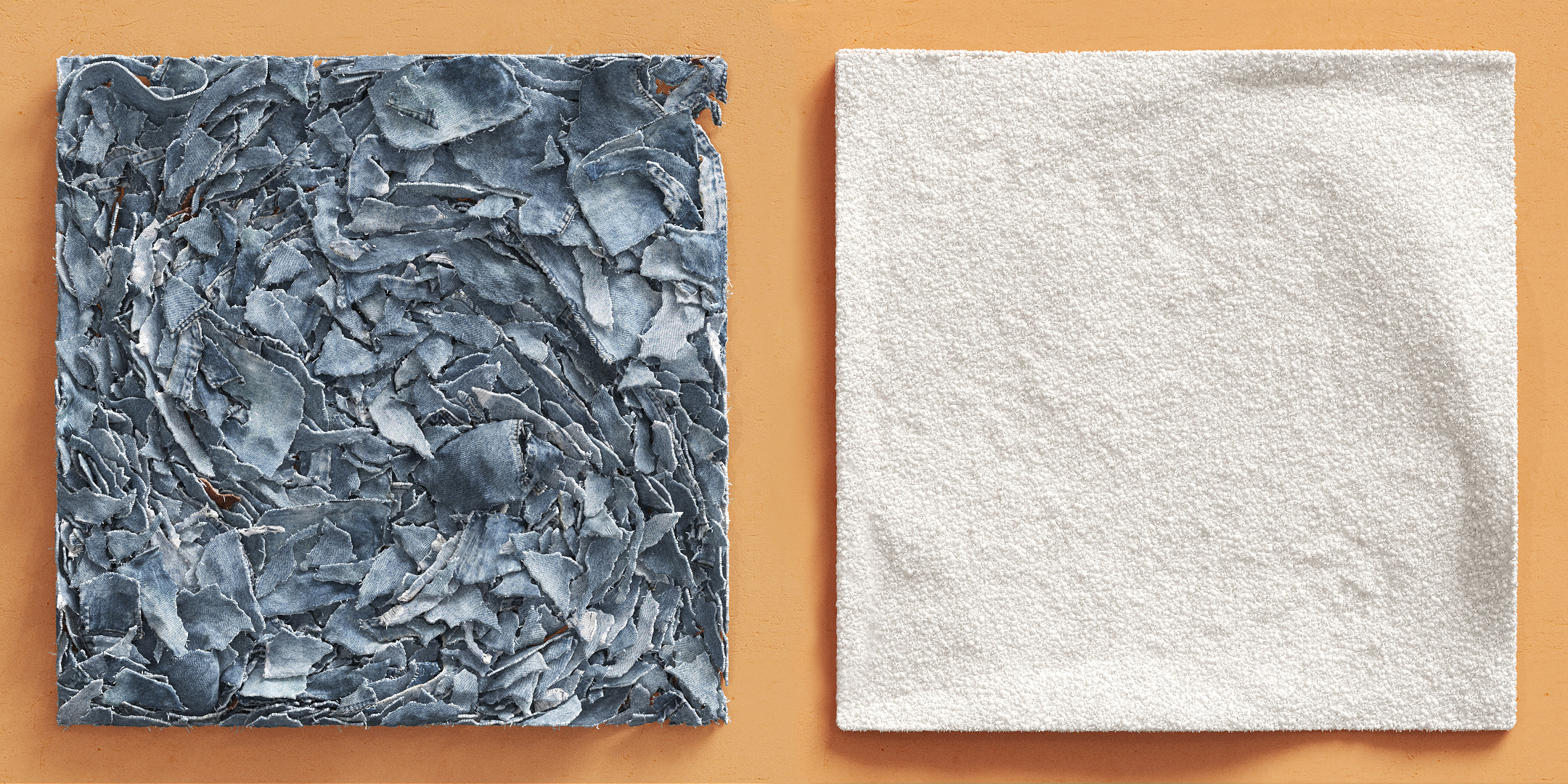
The versatility of cellulosic fibers is being pushed further as waste feedstocks seek to replace resource thirsty plants. We explore how household names and innovative startups are using alternative resources in their fiber innovation.
As one of the most versatile fibers in the market, cellulosics offer both function and comfort, and can be engineered for a range of benefits. New innovations are now entering the market that combine these benefits with circular resources, for a more sustainable alternative. One of the oldest resources, cellulosics in their broadest term incorporates the majority of plant grown fibers. Traditionally these have been used to create natural cotton and linen based textiles, or man-made regenerative alternatives like viscose and modal, which are created from dissolved forms of cellulosics.
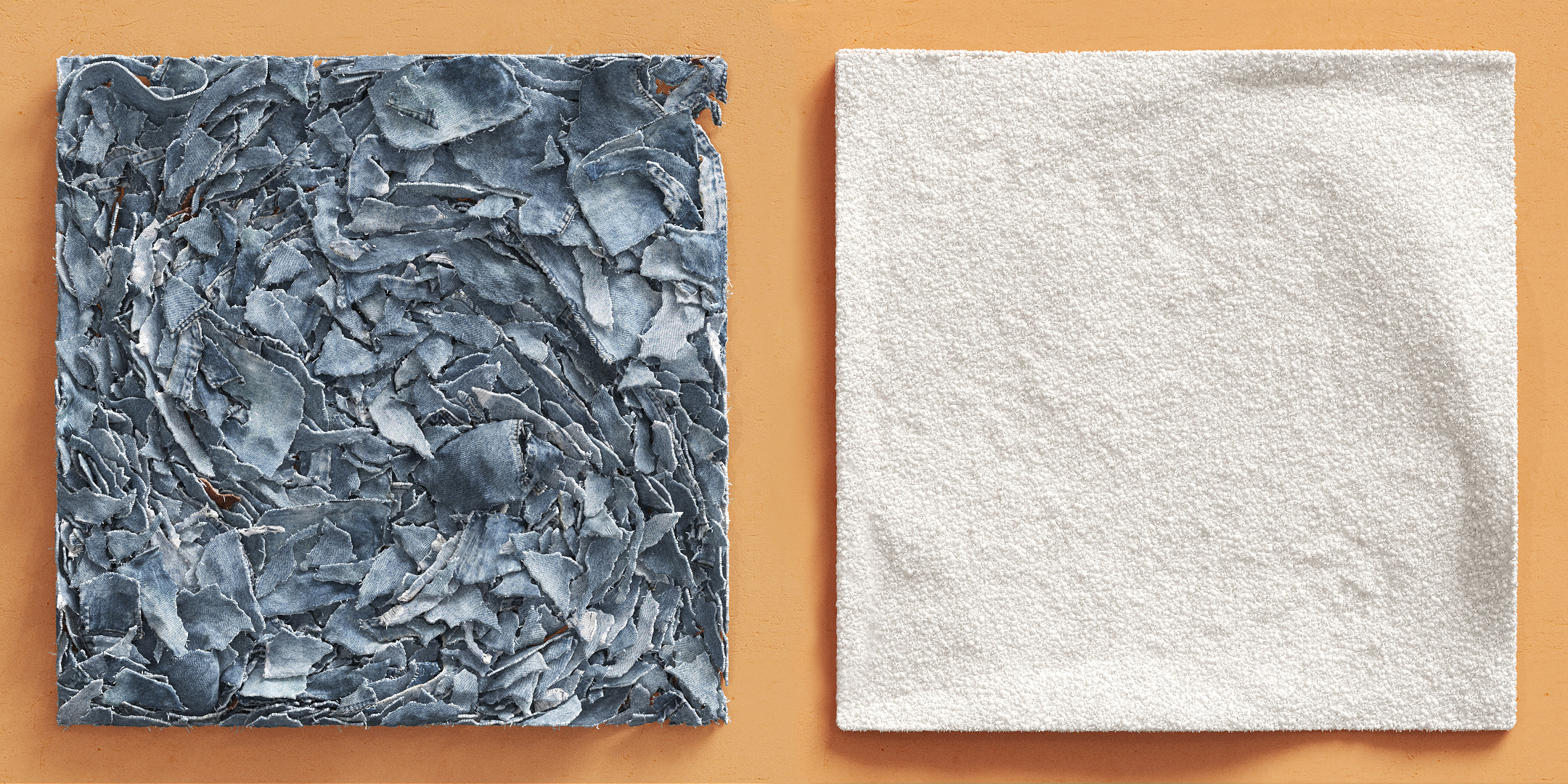
Many cellulosic fibers in the market today are derived from plants like cotton, flax and timber, making them a resource hungry fiber that requires large amounts of land, water and often pesticides. The global fiber industry is currently facing endless challenges, such as climate change, water scarcity and rising populations which raise the question of land usage and biodiversity. Whilst the demand for versatile regenerative cellulosics increases, the global market is expected to grow by 8.1% by 2025, a new alternative generation of regenerative fibers are starting to emerge that mitigate the need for virgin natural resources, looking instead to circularity and agricultural waste. As Alex Ingildsen, CCO at LTP Group states;
“Regenerative raw materials are appealing more and more to the brands we’re working with, ensuring performance benefits such as breathability, wicking, anti-bacterial properties and skin soothing softness. While at the same time allowing brands to move closer to their sustainable goals through the fibers inherent circularity and biodegradability.”
Below, we’ve highlighted some of the top innovations entering the alternative regenerative cellulosics market, all of which are also showcased in our latest edition of the 360° Innovation Book, dubbed IB.05.
Circulose by Renewcell
Swedish based Renewcell is a textile recycling company that has created a way to turn
discarded textiles into new fibers, a process and fiber they have patented as Circulose. Unlike traditional recycling methods, which tend to produce shorter fibers and less uniform textiles, Circulose can offer virgin quality long-length fibers.
The recycling process developed by Renewcell works by extracting cotton from textile waste before using a water-based chemical process to extract cellulose which can then be reused as a replacement for both natural and man-made fibers. Much of this textile waste is post-consumer waste, which once collected has its trims removed before being shredded and contaminants such as polyester removed through the chemical process, leaving just cellulose.
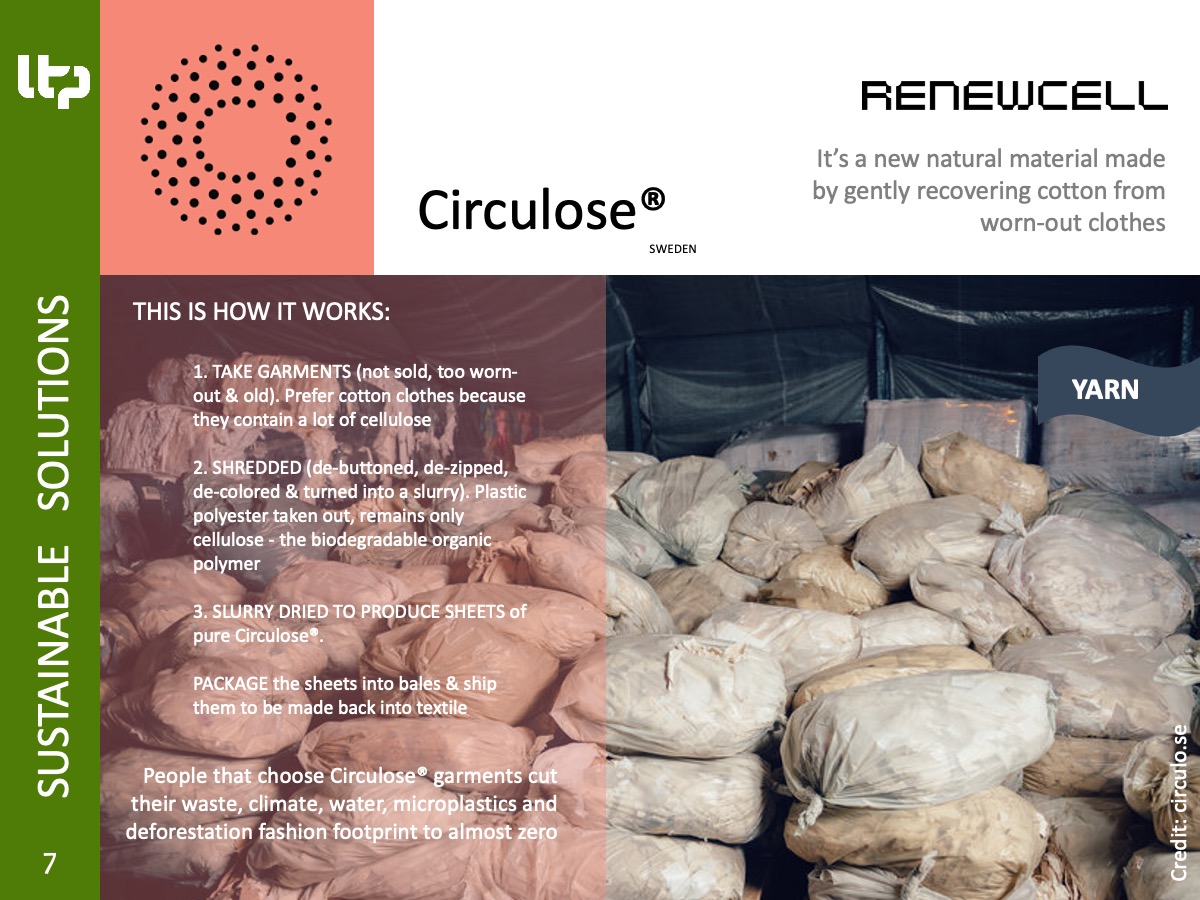
Though an innovative technology, this process of synthetic and natural fiber separation is already being scaled up by Renewcell. In 2020 they were producing 4,500 tons of renewed fiber, with this anticipated to grow to 60,000 by 2025. They also signed a letter of intent in March 2022 with Birla Cellulose, one of the world's largest man-made cellulosic fiber producers - allowing Circulose to be accessed by a wide range of brands and manufacturers.
Nullarbor by Nanollose
If we look to the southern hemisphere, Australian based Nanollose are a company who are innovating by creating cellulosic fibers from pre-consumer food waste, namely coconuts. Their fiber, called Nullarbor, is made by bacterial microbes feeding on the agricultural waste, and through natural fermentation, converting it into microbial cellulose. The process, which takes just 18 days, requires less resources than traditional cellulose. The yield of Nullarbor cellulose is considerably higher than cotton, bamboo and traditional tree based cellulosics, offering up to 32 times the yield of their tree based alternative alone.
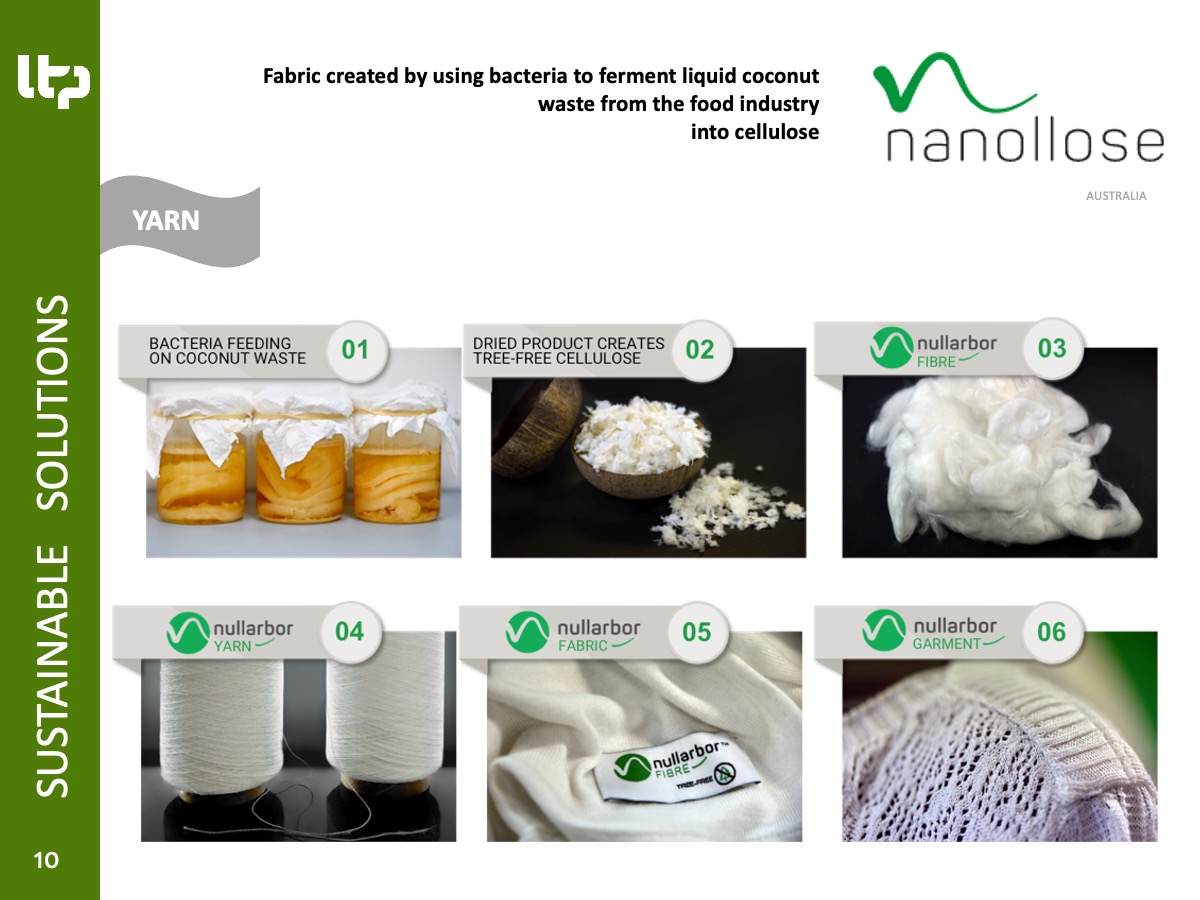
The resulting Nullarbor fiber is resilient and adaptable, and can be used as an alternative to wool, cotton and manmade fibers. Nanollose has now signed agreements with global manufacturing partners, helping to scale up the fiber, yarn and materials presence. Starting to be used commercially, the first garment created using it was made by Australian designer Lee Mathews, and produced using standard industrial equipment, meaning no changes are needed to production processes and Nullarbor fiber can be easily switched in instead of conventional fibers.
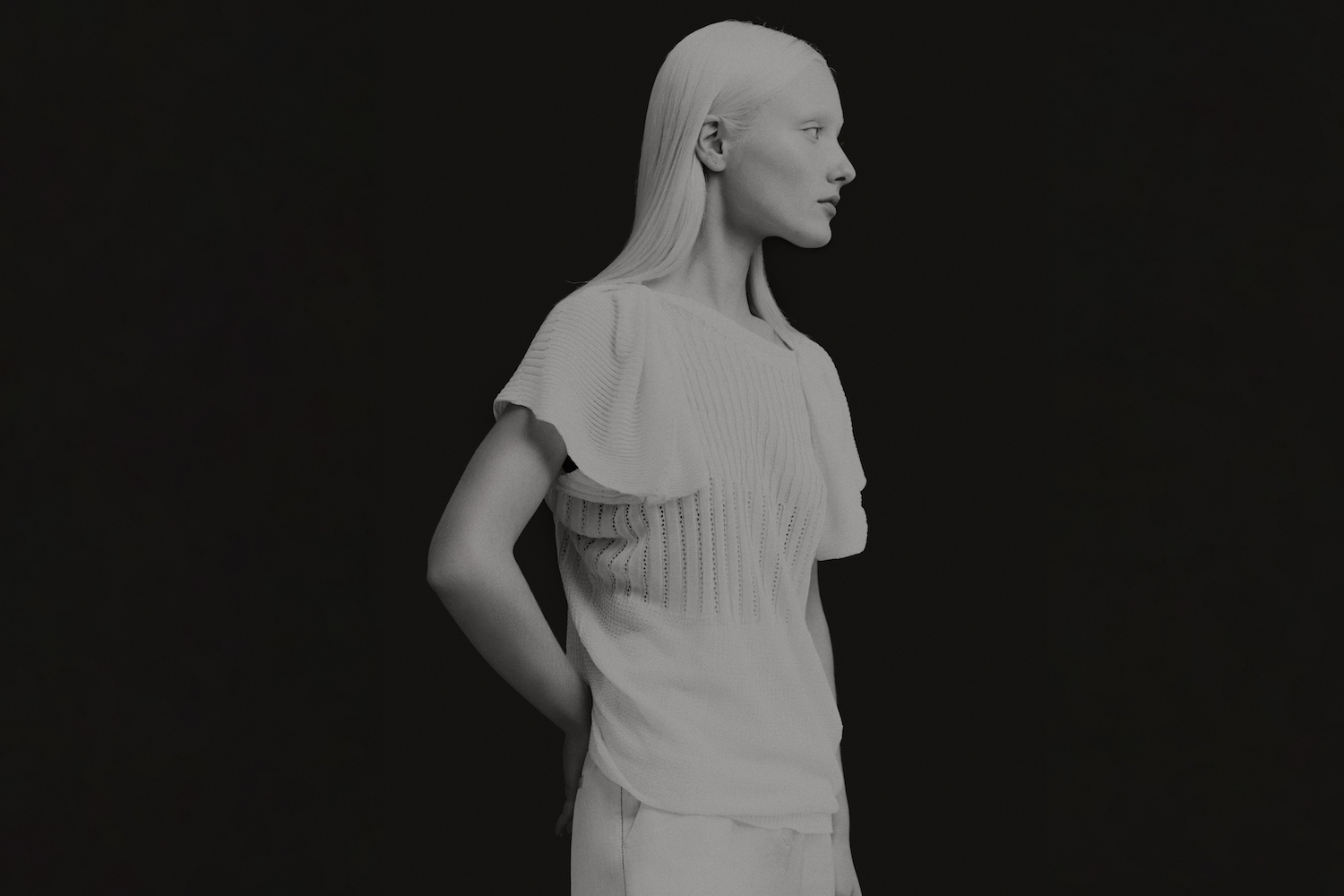
Tencel x Refibra
A leading name in cellulosics, Tencel have created their Refibra technology which makes circular lyocell fibers from cotton scraps, reclaimed from garment production and post consumer waste. The fibers created through the Refibra technology can be used in their pure state, or combined with cotton, conventional cellulosics or elastane, depending on the end usage.
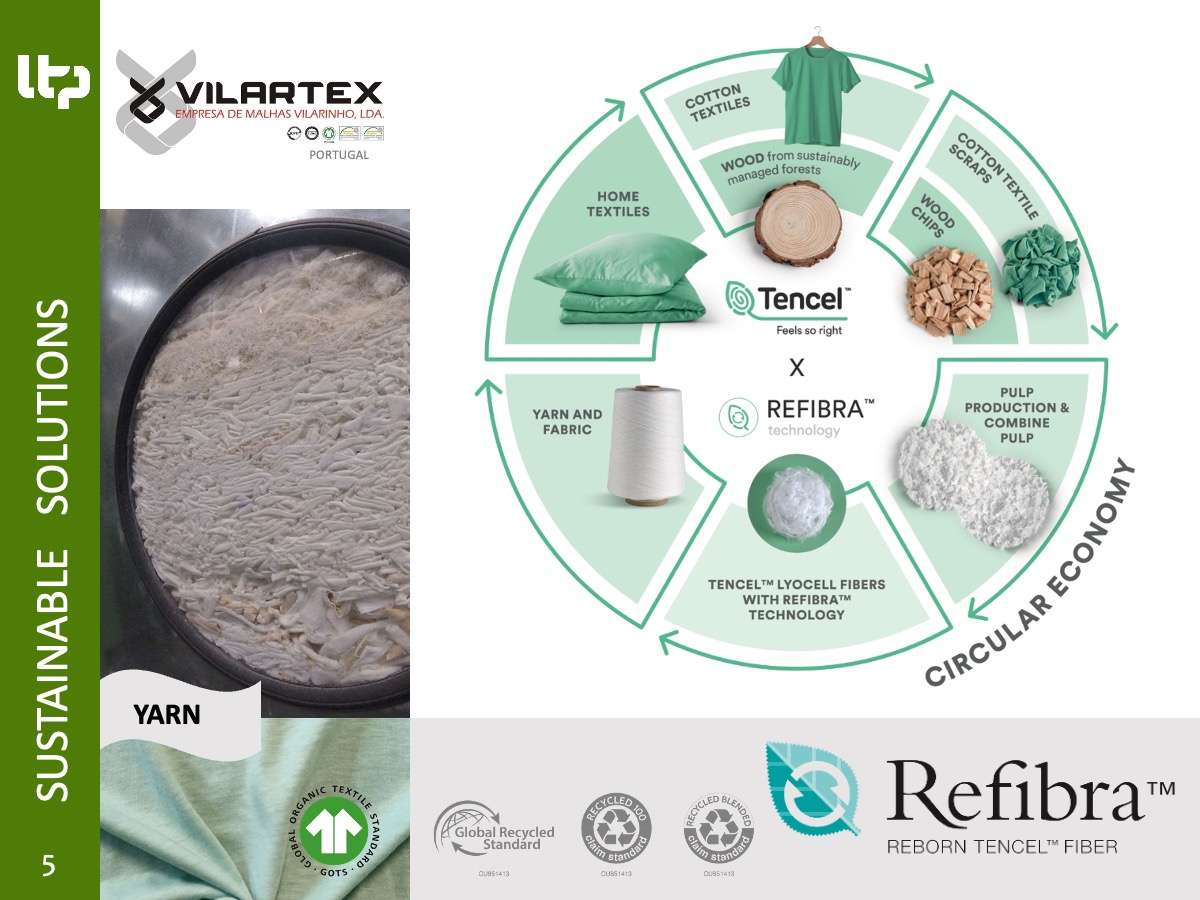
The technology creates a virgin quality fiber, from circular waste, whilst also adding special identification technologies to yarns, fabrics or final garments that state the fiber origin, improving supply chain transparency. Tencel fibers made through the Refibra technology offer virgin quality, whilst being an ecological alternative to resource hungry wood-based cellulose.
As part of the Tencel brand, the reach of fibers made through the Refibra technology is already at a commercial scale, with suppliers such as Sampaio & Filhos, Joaps, Zeynar and Vilartex, using it with a number of their clients and brands. Vilartex in particular have combined Refibra fiber with 70% organic cotton to create a range of different structures that include single jersey, interlocks, fleeces and waffles.
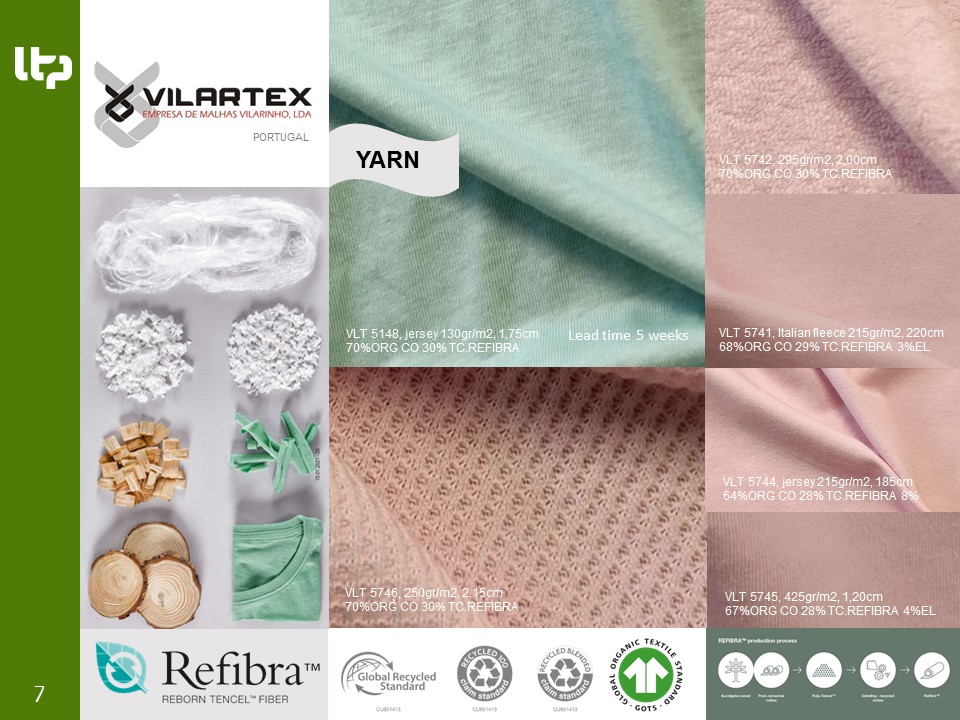
How to get your copy of LTP’s Latest Innovation book
IB.05 showcases the latest innovations in textiles, trims and technologies. To get your hands on a copy of the latest Innovation book, all existing customer should contact Alex.
The Innovation 360° book has become a place for suppliers to introduce their latest “super materials” and pioneering developments. If you’re an innovative supplier and wish to be featured in the next edition, please contact Alex.
This resource is created as part of the companies Value Added Services which are strategically developed to provide brands with the tools to drive new and exciting innovations. This suite includes:
LTP Consciously Crafted
3D Product Visualization
Sustainability Solutions Accelerator
Product Design & Development, Creation and Innovation
360° Innovation book
Seasonal Trend Analysis for the Sport & Outdoor Industry
The Sport & Outdoor Apparel Network
For more information please feel free to contact Alex at the LTP Group [ali@ltpgroup.com].
About LTP
LTP is a Danish owned garment manufacturer for +60 premium brands within active sportswear, cycling, outdoor, urban performance, performance running and organic & lifestyle apparel. LTP was established in 1991 and now spans two continents - Europe and Asia with 6 fully owned factories. Our European Innovation Centre is located in Kaunas, Lithuania and our Asian Innovation Centre is located in Ho Chi Minh City, Vietnam. We have a bluesign partner factory in all 5 countries where we operate (Lithuania, Ukraine, Romania, Belarus and Vietnam).
LTP consists of two divisions; LTP Garment and LTP Furniture producing in eleven fully-owned factories.